Plastic extrusion for streamlined, flexible manufacturing solutions
A Comprehensive Overview to the Process and Benefits of Plastic Extrusion
In the large realm of manufacturing, plastic extrusion arises as a extremely efficient and necessary process. Altering raw plastic into continual accounts, it provides to a huge selection of markets with its impressive versatility.
Understanding the Essentials of Plastic Extrusion
While it may show up complex initially look, the procedure of plastic extrusion is essentially easy - plastic extrusion. It is a high-volume production method in which raw plastic is melted and shaped into a constant account. The procedure begins with the feeding of plastic product, in the type of granules, powders, or pellets, right into a warmed barrel. The plastic is then melted making use of a mix of heat and shear, used by a revolving screw. As soon as the molten plastic reaches completion of the barrel, it is required with a little opening called a die, forming it right into a desired kind. The shaped plastic is after that cooled, strengthened, and cut right into wanted lengths, finishing the process.
The Technical Process of Plastic Extrusion Explained
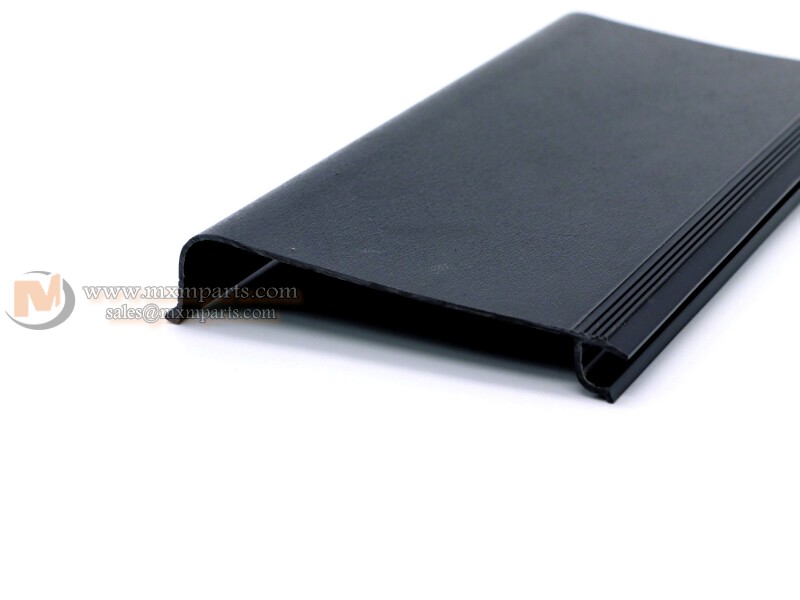
Kinds Of Plastic Suitable for Extrusion
The option of the right type of plastic is a crucial element of the extrusion process. Numerous plastics provide special buildings, making them extra fit to particular applications. Polyethylene, as an example, is typically made use of as a result of its low cost and simple formability. It uses superb resistance to chemicals and moisture, making it excellent for items like tubing and containers. Likewise, polypropylene is one more preferred option as a result of its high melting factor and resistance to fatigue. For even more durable applications, polystyrene and PVC (polyvinyl chloride) are usually selected for their stamina and sturdiness. These are common options, the selection ultimately depends on the certain requirements of the product being produced. Understanding these plastic types can significantly boost the extrusion procedure.
Contrasting Plastic Extrusion to Other Plastic Forming Approaches
Recognizing the types of plastic appropriate for extrusion paves the way for a more comprehensive conversation on how plastic extrusion stacks up against various other plastic creating methods. Plastic extrusion is unequaled when it comes to developing continuous profiles, such as pipes, gaskets, and seals. It also permits for a constant cross-section along the length of the item.
Secret Advantages of Plastic Extrusion in Manufacturing
In the realm of manufacturing, plastic extrusion offers many considerable benefits. One remarkable advantage is the cost-effectiveness of the process, which makes it an economically attractive manufacturing method. In addition, this strategy provides remarkable item flexibility and enhanced production rate, therefore boosting total manufacturing effectiveness.
Economical Production Technique
Plastic extrusion jumps to the leading edge as an affordable manufacturing method in manufacturing. This procedure stands out for its ability to create high quantities of product rapidly and effectively, giving suppliers with significant cost savings. The key price advantage is the capability to make use of cheaper resources. Extrusion uses polycarbonate products, which are click to read more less expensive contrasted to metals or ceramics. Even more, the extrusion process itself is fairly easy, lowering labor costs. Furthermore, plastic extrusion needs less power than traditional manufacturing techniques, contributing to lower functional costs. The process likewise minimizes waste, as find more information any excess or malfunctioning products can be recycled and reused, supplying another layer of cost-effectiveness. Overall, the economic advantages make plastic extrusion a very appealing alternative in the production industry.

Superior Product Versatility
Beyond the cost-effectiveness of plastic extrusion, an additional significant advantage in making lies in its superior item adaptability. This makes plastic extrusion an excellent service for industries that require tailored plastic parts, such as automobile, building and construction, and packaging. In essence, plastic extrusion's item versatility cultivates advancement while enhancing operational effectiveness.
Enhanced Production Rate
A substantial advantage of plastic extrusion lies in its improved manufacturing rate. Few other manufacturing processes can match the speed of plastic extrusion. Additionally, the capacity to keep constant high-speed production without sacrificing item high quality sets plastic extrusion apart from other techniques.
Real-world Applications and Impacts of Plastic Extrusion
In the realm of manufacturing, the strategy of plastic extrusion holds extensive importance. This process is extensively made use of in the production of a range of products, such as plastic tubes, home window frameworks, and weather removing. Therefore, it substantially affects markets like construction, product packaging, and automobile sectors. Its effect extends to day-to-day items, from plastic bags to tooth brushes and disposable flatware. The financial advantage of plastic Learn More extrusion, primarily its high-volume and economical output, has revolutionized production. However, the ecological influence of plastic waste remains a concern. The sector is constantly aiming for developments in eco-friendly and recyclable materials, indicating a future where the advantages of plastic extrusion can be retained without compromising environmental sustainability.
Verdict
To conclude, plastic extrusion is a highly effective and effective approach of changing resources into diverse items. It offers countless benefits over other plastic forming techniques, including cost-effectiveness, high output, marginal waste, and style versatility. Its effect is profoundly felt in numerous sectors such as construction, vehicle, and durable goods, making it a crucial procedure in today's production landscape.
Delving deeper into the technological process of plastic extrusion, it begins with the option of the appropriate plastic product. Once cooled down, the plastic is cut into the called for lengths or injury onto reels if the product is a plastic film or sheet - plastic extrusion. Comparing Plastic Extrusion to Various Other Plastic Forming Approaches
Understanding the types of plastic ideal for extrusion paves the means for a broader conversation on exactly how plastic extrusion piles up against various other plastic creating techniques. Couple of other production procedures can match the speed of plastic extrusion.